This UBC professor is spinning the stuff of electric dreams
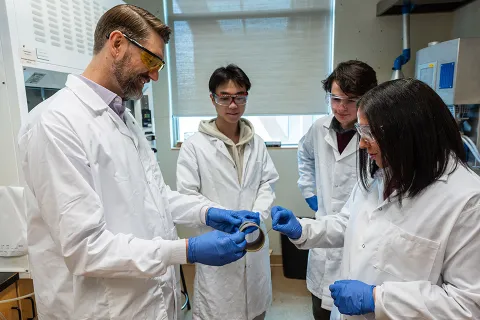
December 6, 2023: Since this article was first published, Dr. Yasmine Abdin's project was as one of five successful projects selected for Phase III of the Carbon Fibre Grand Challenge, and the only one led by a university. Dr. Abdin's team is receiving $4 million in funding.
A new process developed at UBC to make lightweight electric cars is steering closer to reality.
At her lab in the Faculty of Applied Science, UBC materials engineering assistant professor Dr. Yasmine Abdin and her collaborators, Dr. Frank Ko and Dr. Scott Renneckar, have successfully transformed bitumen into carbon fibres – spinning the black, sticky substance from Alberta’s oil sands into a crucial product for the energy transition.
Compared to gasoline-powered cars, battery electric vehicles can be hundreds to thousands of pounds heavier due to the weight of their batteries. As Dr. Abdin, the project lead and an expert on polymer-based composite materials, explains, “Building a car’s chassis or body with lightweight carbon fibres not only helps to compensate for a heavy EV battery pack, the carbon fibres also enhance a battery’s ability to stay cool, improves passenger safety and extends driving range.”
Unlocking value from waste
Known for their durability and light weight, carbon fibres not only enhance the performance of auto parts but also find applications in everyday products like tennis racquets, skateboards and hockey sticks.
However, producing carbon fibres is notoriously expensive, with about half of the cost attributed to the raw material, polyacrylonitrile (PAN), a type of polymer resin. By switching to bitumen, costs can be significantly reduced while also mitigating the environmental impact associated with bitumen, which releases carbon dioxide when burned.
Dr. Renneckar, a professor in the department of wood science at UBC and the Canada Research Chair in Advanced Renewable Materials, notes that significance of the new process. “We are re-purposing what is essentially a low-value product that can cause environmental damage, to produce materials that will enable clean tech.”
Cheaper, finer fibres
The process developed by Dr. Abdin and her colleagues was one of the winning solutions during the first two phases of the Carbon Fibre Grand Challenge, a competition launched by Alberta Innovates to recover valuable products from oil sands, and was recently described in Advances in Natural Sciences: Nanoscience and Nanotechnology.
At the core of the successful UBC formula lies a process that is not radically different from how carbon fibres are currently made, but in a unique method of spinning finer fibres while maintaining the fibres’ structural integrity. Additionally, the UBC team has developed two distinct fibre sizes — regular micro-diameter fibres, and nano-fibre structures, both derived from bitumen.
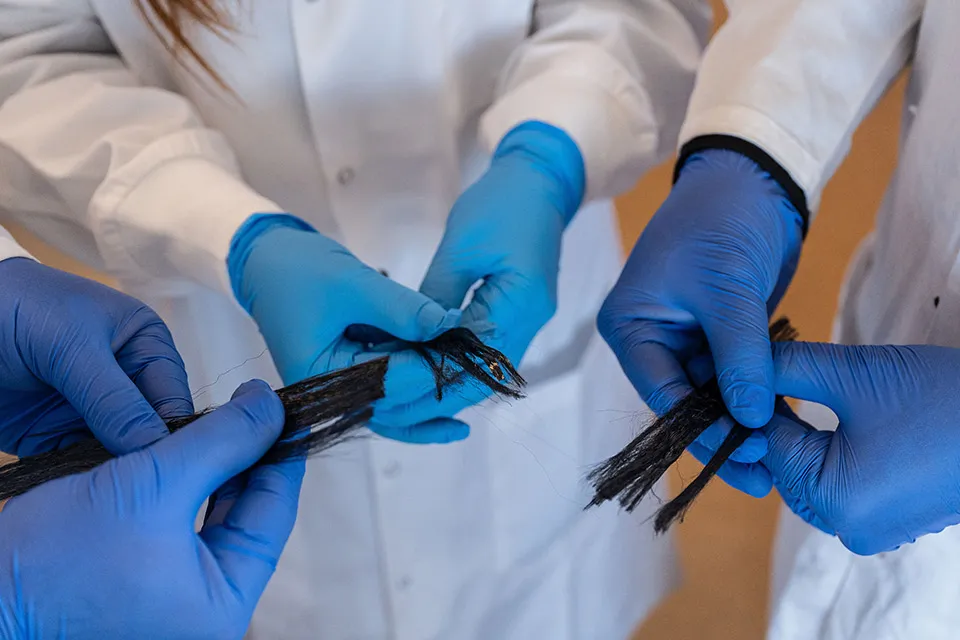
Significantly, the team’s process enables the production of carbon fibres for less than $12 per kilogram, in contrast to the typical commercial rate of $33 per kilogram.
“With a price point of $12 per kilogram, high-volume industries like automakers will have the opportunity to use more carbon fibres,” said Dr. Abdin. “Currently, composite materials like carbon fibres comprise only about 15 per cent of a car’s composition. Affordable carbon fibres can potentially double this figure, which could be a game changer.”
Canada manufactures around one million cars and other light vehicles annually. If automakers can use carbon fibres in most of these vehicles, Canadian manufacturing will gain a competitive advantage, adds Dr. Abdin.
Contributing to net-zero goals
Dr. Abdin and her team plan to apply for the third phase of the Carbon Fibre Grand Challenge competition, which will involve testing of the fibres on a larger scale, ultimately leading to commercial-scale production.
The additional funding in the third round will facilitate scaling up fibre production and the manufacturing of composite products.
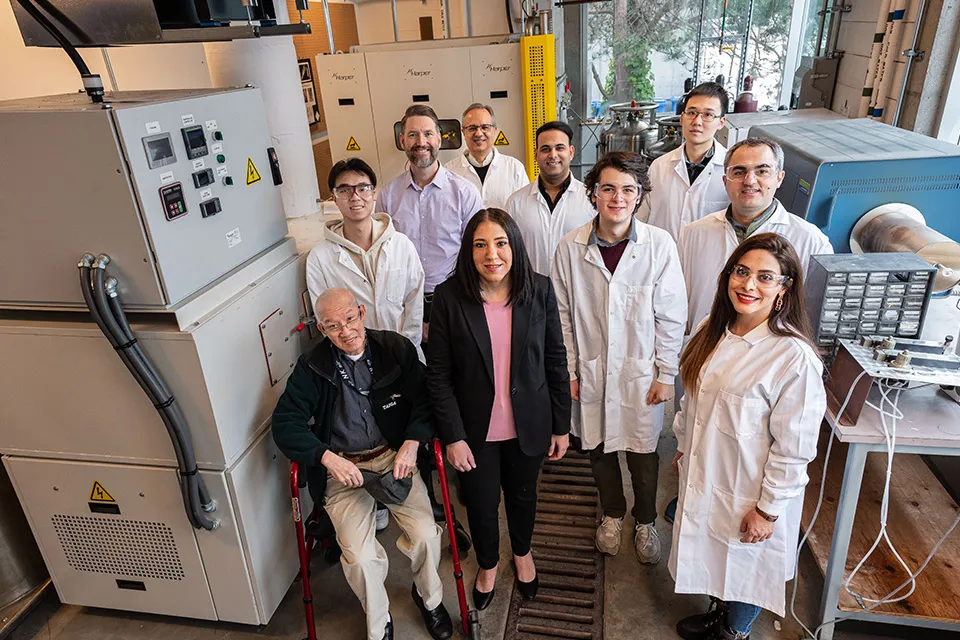
“The world needs more affordable carbon fibre and Alberta’s bitumen is the ideal feedstock,” said Bryan Helfenbaum, associate vice president for clean energy at Alberta Innovates. “The Carbon Fibre Grand Challenge accelerates the development process for manufacturing carbon fibre from Alberta bitumen. Innovators will move closer to commercializing the production of carbon fibre from bitumen by the end of Phase III of this competition.”
Twelve teams were funded in phase two, but only five or six teams will be funded for the final phase. With $4 million in funding at stake, Dr. Abdin is gearing up for the future.
“Automakers aren’t the only industry we’re targeting with the cost and performance benefits of our fibres. We’re also exploring wider applications in wind turbines, structural batteries, supercapacitors, pipelines and even hockey sticks!”