
Jaclyn Canlas, Joshan Gill, Clara Lo, Alex Martinez and Lohita Swaminathan
- Degree: Bachelor of Applied Science
- Program:
- Campus: Vancouver
Our project
We designed and built Injection Buddy, a robotic arm that administers subcutaneous injections for people with mobility challenges.
This device targets individuals with rheumatoid arthritis – who often have limited dexterity – who could use Injection Buddy to safely self-administer injections in the comfort of their own home.
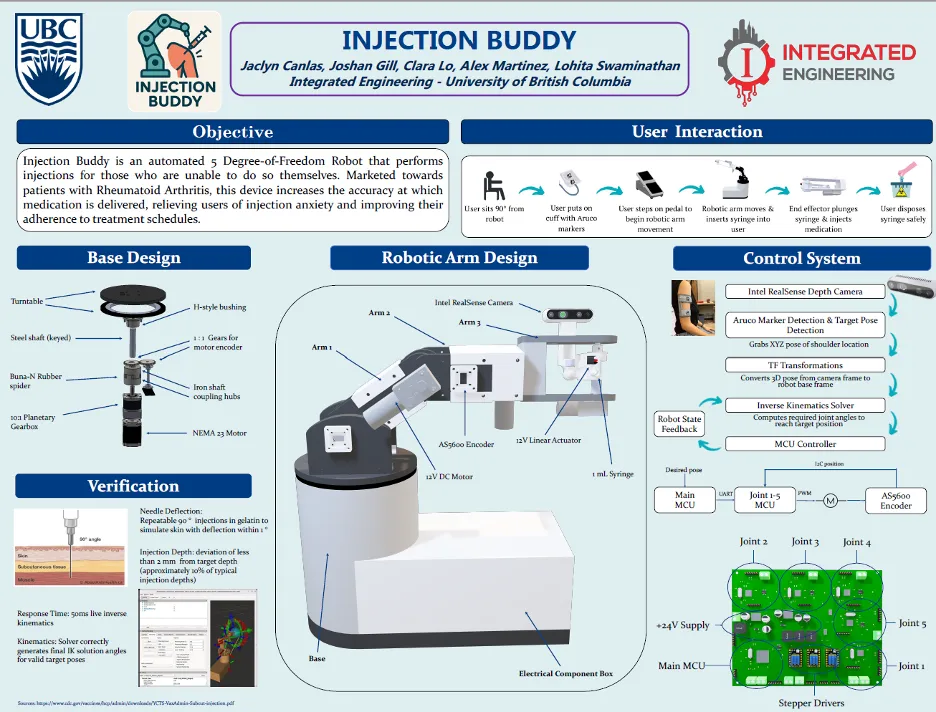
The challenges we faced
The fabrication of the arm and assembly took longer than expected. This created a time crunch later in the process – the longer it takes to set everything up mechanically, the less time you have to finetune the electrical and software systems.
We were working within a very tight budget to build our device. This challenge created an opportunity for us to be innovative in our approach.
For example, it’s common for robotic arms to use a stepper motor and gearbox to provide the torque needed to move the arm. But this combination of components is very expensive, costing around $120 per joint. Instead, we used a different type of motor and then added a component that – combined with our software – made the motor much more precise and provided the torque we needed at about $40 per joint.
What we’re most proud of
We built everything ourselves: we designed every joint, machined the parts and put it all together; created our own circuitry and built a custom control board capable of controlling six different motors simultaneously; and learned about vision systems and coded everything on the software side. This made it all the more meaningful when we got our device to work and repeatedly injected a syringe within a narrow radius.
We collaborated to solve problems and achieve full system integration. For example, there were times when the motors were not able to lift up the arm, and we had to work together to address mechanical and electrical issues.
We embraced a fluid and dynamic design cycle, and we were all committed to persevering to develop creative solutions to make our device the best it could be.
On the software side, after doing all the work on calculations, vision system, coordinate transformations, inverse kinematics and serial communication and testing it through simulations, it was very rewarding to see that work come to life and be translated into movement of the robotic arm.