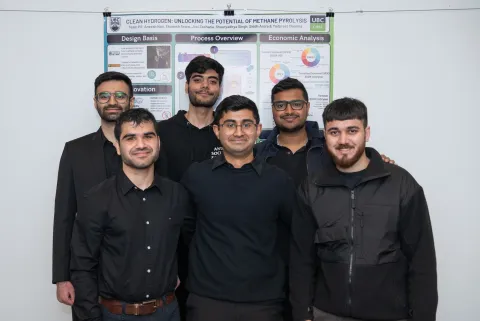
Ekaansh Arora, Siddh Arora, Yadpreet Cheema, Aneesh Nair, Shauryaditya Singh, Joel Zacharia
- Degree: Bachelor of Applied Science
- Program:
- Campus: Vancouver
Our project
We designed a sustainable low-emission hydrogen production facility in Kitimat, BC. Our molten metal methane pyrolysis process produces high-purity hydrogen for applications such as fuel cell vehicles and natural gas blending, along with solid carbon suitable for use in battery anodes, rubber and composite materials.
By integrating advanced technologies such as bubble column reactors, cyclonic carbon separation and pressure swing adsorption units for hydrogen purification, our project contributes to the growing hydrogen economy while promoting environmental stewardship.
Our design solution and process
Traditional methods for producing hydrogen are very resource intensive. Steam methane reforming can emit eight to 12 tonnes of carbon dioxide per tonne of hydrogen produced, and electrolysis is extremely energy intensive. For example, a proposed green hydrogen ammonia plant in Prince George based on electrolysis would require 90% of the electricity produced by the newly operational Site C dam.
Many studies – such as the 2024 report The Potential for Methane Pyrolysis in B.C – have shown that methane pyrolysis is a cost-effective way to produce low-carbon-intensity hydrogen in BC given our abundant natural gas supply. Methane pyrolysis produces hydrogen by breaking methane into hydrogen and solid carbon. It does not produce carbon dioxide as the produced carbon is in solid form.
One of the major technical challenges to resolve before hydrogen can be produced via this pathway at an industrial scale is carbon coking. Our design addresses this challenge by combining a bubble column reactor and a molten metal catalyst.
Our process begins by preheating the feedstock to 700°C. It then enters a bubble column reactor and passes through a sparger to transform the gas into bubbles. The methane bubbles react on the molten metal catalyst layer to form hydrogen with solid carbon (90% graphite and 10% carbon black) as the byproduct.
We separate the hydrogen and carbon using an innovative cyclonic separation process. We then purify the hydrogen using two pressure swing adsorption columns to the 99.9% purity required for hydrogen fuel cell applications. Our proposed plant design will require 77,000 tonnes of natural gas per year to produce 18,250 tonnes of hydrogen and just under 55,000 tonnes of solid carbon byproduct.
As part of this project, we developed a plant layout, piping and instrumentation guidelines, start-up and shutdown procedures, a hazard and operability analysis, environmental assessment and an economic analysis that identifies potential funding sources and includes revenue estimates and a sensitivity analysis.
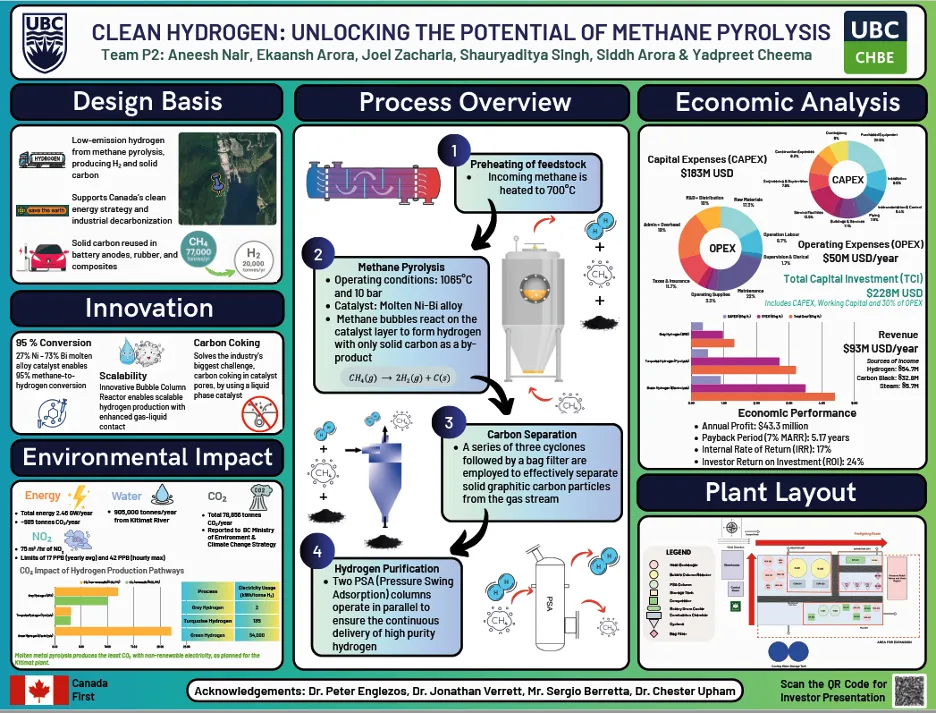
Our project’s future
While there have been some advances on producing hydrogen using methane pyrolysis, much more work needs to be done to take it to the next step. Our work could represent an important advancement of knowledge to bridge the gap, particularly given the level of detail we’ve developed around control strategies. More work will need to be done to make this a viable project.
It was extremely important, to us, to make this a Canadian focused project that prioritizes Canadian products and looks into the best interest of our great country.
We source natural gas from BC or Alberta, use Canadian-made industrial steel for the bubble column reactor, and rely on domestically produced nickel-bismuth for the catalyst. The hydrogen generated will be blended into the FortisBC supply, reducing emissions from natural gas use and supporting the province’s clean energy goals.