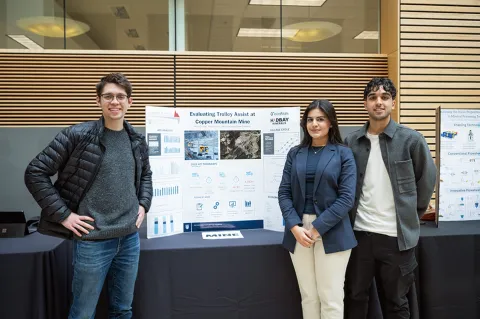
Dane Campbell, Arjun Chahal, Sanya Dua and Mani Nassiri
- Community Partner: Atkins Realis and Hudbay
- Degree: Bachelor of Applied Science
- Program:
- Campus: Vancouver
Our process and the results of our analysis
At the start of the project, we travelled to Princeton, BC, to tour the Copper Mountain Mine. This is a conventional open pit mine with daily mill capacity of 45,000 tonnes. The main pit includes a trolley assist system whereby trucks are attached to a electric trolley line to help them up a one-kilometre ramp.
After visiting the site and talking with our client about their goals for this project, we submitted requests for information for the data needed to complete our analysis.
We reviewed the data packages and then used Python and Excel to conduct an analysis of key performance indicators for utilization and mechanical availability, operating delays, cycle time and production. This included getting comparable data from other trucks on site that do not use trolley assist system.
Our haulage analysis showed that the trolley-assisted fleet has 16% higher utilization availability and five minutes less delay time per operating hour than conventional trucks. Our financial analysis showed haulage cost savings of 4.8% (per tonne moved), primarily as a result of removing up to 97% of diesel fuel costs for that one section of ramp.
We also found that the trolley system adds value in terms of production. The trolley-assisted trucks can travel up the ramp at speeds reaching 24 km/hour, compared to 10-15 km/hour for diesel trucks. This enables the trucks to move more ore, and the reduced standby hours compared to diesel trucks (which require refuelling time) also contributes to higher production.
Our analysis enabled us to calculate that the breakeven ramp length is equal to 1930 meters at a 10% grade and over 10-year asset life.
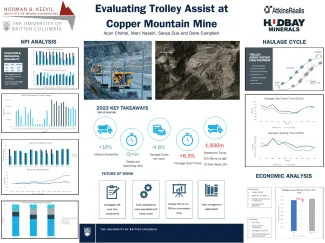
What we’re most proud of
It was great to work closely with the team at the mine site and to dive into the details of the trolley assisted system.
Although the technology has been around a long time and is used in many applications, this was the first time a mine in Canada took a leap on this technology. HudBay had already calculated the impact of this investment on carbon emissions, and our work broadened that so we can preliminarily recommend the system for ramps that are over two kilometres long due to its positive impact on operations and financial performance.