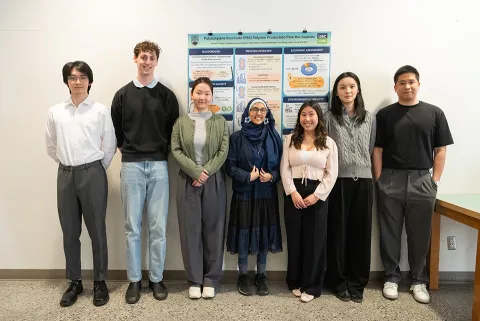
Yuting Ji, Pachara Lobunchongsook, Ethan Markey, Umamah Mokarram, Terry Wong, Lauren Young and Ella Zhou
- Degree: Bachelor of Applied Science
- Program:
- Campus: Vancouver
Our project
Plastics are a problem. At the end of their life – which for many plastics is only a one-time use – the majority of plastics are landfilled or discarded, where they break down into harmful microplastics that pervade our ecosystems and bioaccumulate in food chains. To address this issue, we developed a process and designed a theoretical plant to develop polybutylene succinate (PBS), a biodegradable bioplastic that quickly and naturally breaks down into water and carbon dioxide.
The challenges we faced
As chemical engineering students, we are system thinkers who look at big processes and consider the lifecycle of real-world problems that need to be addressed from start to finish.
That means we consider everything from where the plant is located and its energy and materials requirements to the biodegradability of our product and the policies that must be in place to implement this process in profitable and beneficial ways. It can be a challenge to tie everything together.
Our project is a theoretical process and plant design based on our research. We know we have the correct reactions, conditions and catalysts, but we don’t know the specific optimal parameters of our process. To gain this understanding, we would need to conduct lab-scale experiments and then scale them up to see how they perform in a commercial capacity.
Our project is also limited by the current state of knowledge of PBS’s biodegradability. Our research suggests that under optimal conditions (high temperatures, high moisture content and high microbial activity) PBS plastic in a natural environment could biodegrade in a six-month to five-year period, and in an industrial composting facility it could biodegrade as quickly as in a few weeks. However, as a baseline plastic, PBS would need to undergo further treatment or processing for its end application, which could decrease its biodegradability.
Our project’s future
While research into biodegradable bioplastics has become increasingly popular, further research is still required and industry still faces issues implementing these products on a larger scale.
There is an incredible opportunity to expand the research and market of bioplastics, given how reliant we are on plastics for their versatility and the profound environmental harms that come from traditionally made plastics.
Could there be a time in Canada and the world when, rather than PET plastics, the plastic market is dominated completely by bioplastics? The process and plant design we’ve proposed could also be very valuable in countries that currently have less infrastructure in place to support plastics recycling. Our product could biodegrade in just a few months, without leaching microplastics or harmful chemicals into the land or water.