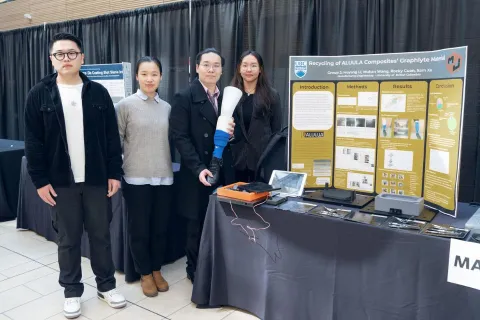
Rocky Guan, Muyang Li, Muhan Wang and Sam Xu
- Community Partner: Aluula Composites
- Degree: Bachelor of Applied Science
- Program:
- Campus: Vancouver
Our inspiration
We were all excited to work on a project that contributes to reduced waste and extends the life of a material for other useful purposes.
Each of us was inspired by different aspects of the project.
What excited us most
It was fantastic to be able to work closely with this very cool composite material from ALUULA and to work with instruments and equipment that most undergraduate students do not normally have a chance to use, such as the hot press machine, the thermogravimetric analyzer (TGA) and differential scanning calorimetry (DSC).
Other aspects of this project that were very rewarding included seeing the progress of our idea from brainstorming concept to product; working with different testers and machines – including the hot pressing machine, Instron mechanical tester and fixtures (tensile, bending, compression), and the TGA and DSC; and recognition from both the client and our supervisor and feeling that we are creating value for the client.
Our project’s future
Our work shows that it is indeed feasible to recycle and reuse ALUULA’s Aeris material at the end of its life cycle.
Our student engineering team will donate the group’s hot press mold, product samples and manufacturing plan to ALUULA Composites. We hope that our work will provide a foundation for the client to promote their commitment to sustainability and extend the use of their materials by producing value-added products like shin pads or other items.