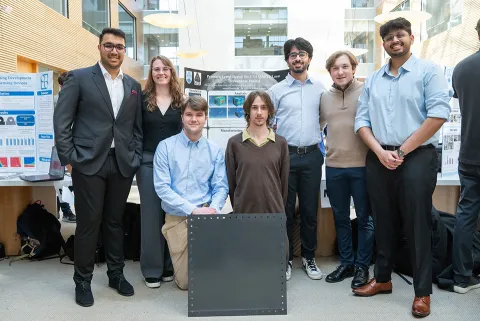
Dominik Adriany, Krish Arora, JP Kahlert, Dylan Kipp, Peter Landine, Veer Sambaragi and Usama Seifeddine
- Community Partner: Canadian Space Agency
- Degree: Bachelor of Applied Science
- Program:
- Campus: Vancouver
Our project
The challenges we faced
We were integrating the work of six other capstone teams from across Canada, which led to logistical issues and delays when teams didn’t deliver designs according to schedule or altered their initial design dimensions. However, being responsible for integrating the work of the subteams was a great learning experience of what it is like to be part of a complex engineering project.
There were some challenges with selecting materials that met the design criteria of being moisture resistant, able to support mechanical and structural loads, able to be pressurized and able to operate within a defined vacuum environment.
We also needed to choose materials that were food safe and that had minimal off-gassing, which limited our choices.
There were also challenges manufacturing the assembly due to some warpage of the plates, which has required additional machining so the components all fit together.
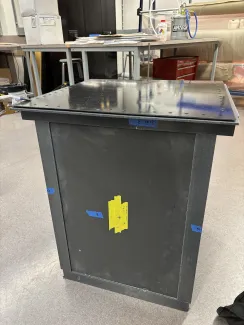
Our project’s future
We will be shipping our prototype to the Canadian Space Agency in Montreal. The agency will integrate the work from the other design teams, mounting their systems into our vessel and then pressurizing it and running tests to simulate several cycles of the moon’s nights and days. Our understanding is that there will be further iterations of the project and other elements will be incorporated, such as the airlock design.