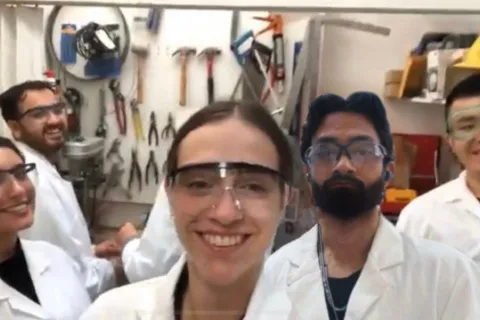
Ailish Chauhan, Teodora Cosovic, Shahil Hamid, Arnav Kapur, Anshul Khattar and Chuanhao Xu
- Community Partner: WorldView
- Degree: Bachelor of Applied Science
- Program:
- Campus: Vancouver
Our inspiration
The CEO of World View shared his vision with us that taking people to the edge of space can help deepen understanding and appreciation of everything we have on earth. The company’s desire to reduce their carbon footprint and repurpose and reuse their single-use materials is part of that vision.
What excited us most
The project brought together everything we’ve learned over our degree for the last four years. It was very fulfilling to design the entire process, end to end – from initial idea to developing a process and then producing the final product.
It was exciting to learn about World View’s vision for space tourism and hear their leaders talk about making their business as sustainable as possible. Networking and learning from others – not just our supervisor Dr. Sergey Kravchenko, but also a PhD student working with him who helped us with the model and Dr. Marek Gnatowski at Polymer Engineering – was also a highlight.
Our project’s future
We delivered the proof of concept to World View. The next step would be additional research on material development to produce parts that have more applications or that are stronger. We used an SLA 3D printed mould to produce the part, but a CNC mould would be preferable in terms of durability and the ability to scale up production.