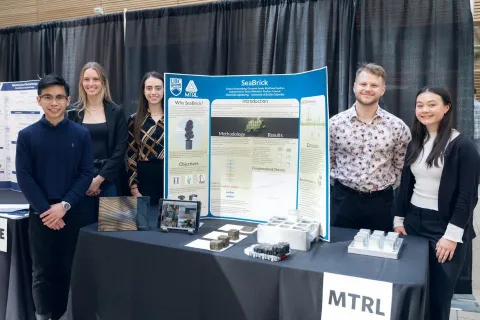
Teodora Cosovic, Giovanna Janes, Sydney Kusch, Matthew Paulino, Colton Routtenberg and Taylor Wheatley
- Community Partner: SeaBrick
- Degree: Bachelor of Applied Science
- Program:
- Campus: Vancouver
Our inspiration
Cement production accounts for eight percent of global carbon emissions, making it one of the largest contributors to the climate crisis.
When concrete is used in marine environments, it can also be very damaging to the environment, with chemical leaching increasing alkalinity and potentially harming ocean life.
Made from kelp, seabricks address the pressing need to decarbonize the marine and construction sector. Whereas a cubic metre of concrete emits 250 kilograms of carbon, a cubic metre of kelp will sequester about 200 kilograms of carbon.
UBC’s efforts towards green concrete
What excited us most
It’s exciting to think of a future where you could build infrastructure with a readily accessible material like kelp.
It was great when our product started to feel like concrete, rather than some of the earlier versions that were a little soft and not suitable for building anything supportive! There was definitely excitement – and relief – when the compression testing results started reaching the number we were aiming for and we realized this could be viable.
In fact, our sponsor has been in discussion with architecture firms that are interested in using a product with these properties.
Our project’s future
No one knew the answer, but everyone was very supportive and rooting for us to succeed.
We made a lot of progress on the solution but weren’t able to achieve the density required for it to be used in floating marine infrastructure. We put together a long list of recommendations in three categories for future research regarding composition, manufacturing and testing.
We owe a lot of thanks to Dr. Jon Nakane and our project sponsor John Richardson. We all felt very lucky to be part of such a hands-on project. Everyone was so willing to help us out – whether that was our sponsor sending us articles and research, getting access to equipment at UBC or our profs asking if we had considered a certain approach.